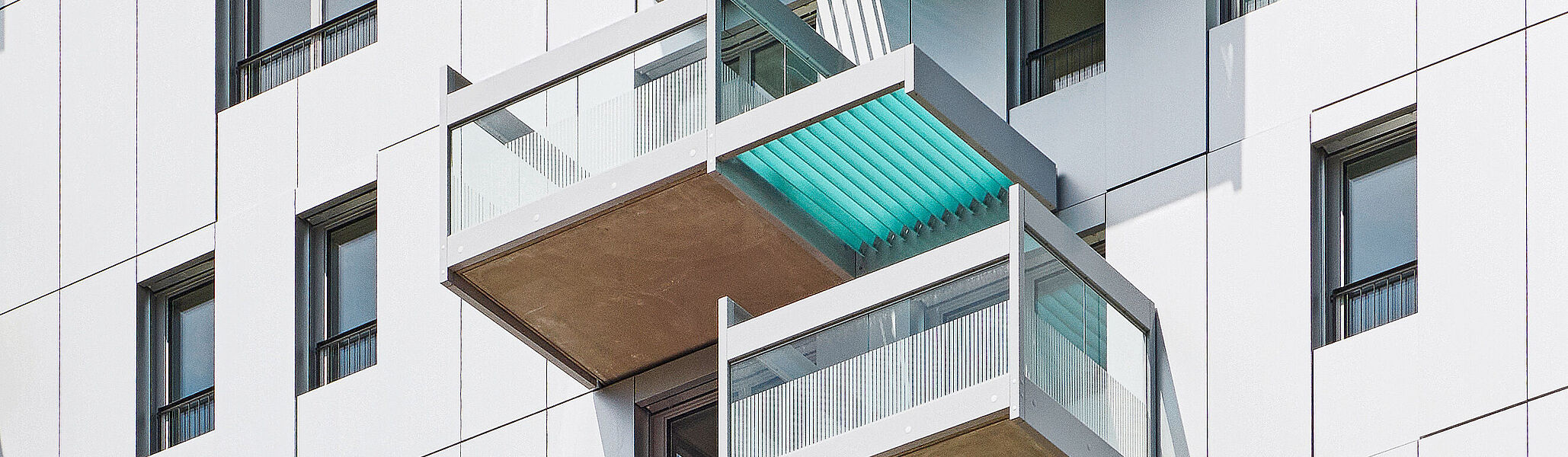
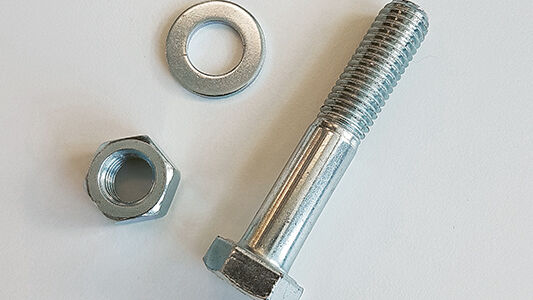
Revêtements de surface pour éléments d’assemblage
Traitements de surface
Les revêtements de surface servent en premier lieu de protection anticorrosion. Un second aspect essentiel est le réglage d’une plage de valeurs de friction afin d’obtenir une précontrainte minimale déterminée pour un couple de serrage donné. L’apparence peut également être décisive pour le choix de la finition de surface.
Connexion
Merci de l’intérêt que vous portez à nos contenus. Les abonnés de la revue spécialisée metall trouveront le Login pour l’accès intégral dans les informations légales de la version imprimée actuelle. Le mot de passe change tous les mois.
Inscrivez-vous maintenant pour lire cet article. Inscrivez-vous pour lire les différents articles et payez très facilement par carte de crédit. (CHF 5.- par article)
En tant qu’utilisateur enregistré, vous pouvez accéder à tout moment à l’article acheté.
Si - en tant que professionnel dans les domaines de la construction métallique, en acier et de façades - vous n’êtes pas encore abonné à la revue spécialisée metall, ne perdez plus une seconde et souscrivez dès à présent votre abonnement ici.
La pratique montre qu’il est pris le plus grand soin au bon choix des dimensions, à la classe de résistance et au frein de vis lors de la conception d’éléments d’assemblage, mais qu’il n’est en général pas attaché assez d’importance à la finition de leurs surfaces. Cette situation est fréquemment à l’origine de dommages précoces causés par la corrosion ou de fractures de vis dues à la fragilisation par l’hydrogène. Il résulte alors la plupart du temps des coûts consécutifs très élevés en raison de la défaillance de l’ensemble de la construction ou du remplacement nécessaire des éléments d’assemblage. Les systèmes de revêtement les plus importants en théorie seront décrits dans le présent article et seront illustrés par des essais pratiques.
Systèmes de revêtement déposés par galvanisation selon SN EN ISO 4042
Il s’agit dans ce cas d’un processus électrolytique. La pièce sert de cathode, différentes anodes en zinc sont utilisées selon le type de revêtement. Les systèmes de revêtement les plus usuels sont le zinc et les alliages en zinc-fer et zinc-nickel. D’autres revêtements possibles sont le cadmium, le nickel, le chrome, le cuivre, l’argent, l’étain et leurs alliages. Des couches de conversion, des scellements et des couches de finition supplémentaires accroissent considérablement la protection anticorrosion et augmentent simultanément la résistance mécanique, celle aux produits chimiques ainsi que la stabilité thermique. Des lubrifiants intégrés ou appliqués ultérieurement permettent de régler une plage de valeurs de friction. Les revêtements en zinc, alliages de zinc et cadmium offrent de plus une protection cathodique en cas d’endommagement du revêtement. Le chrome (VI) n’est déjà plus très utilisé, raison pour laquelle les couches de conversion libres (passivations) utilisées sont aujourd’hui presque toutes exemptes de ce métal. L’illustration a) ci-dessus montre la structure fondamentale des systèmes de revêtement galvanique.