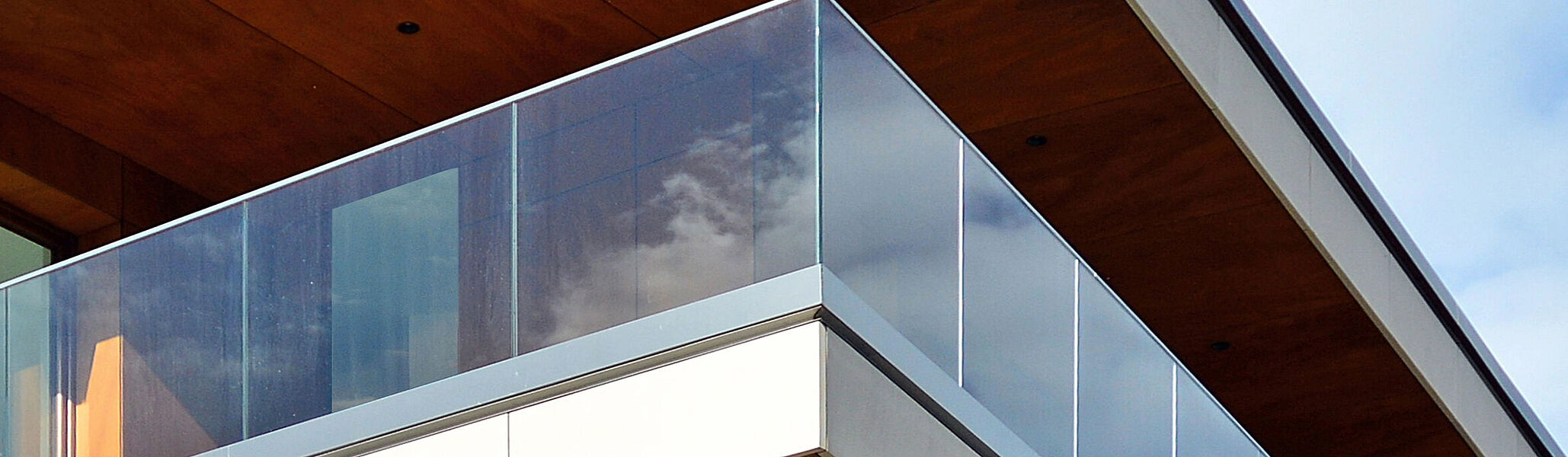
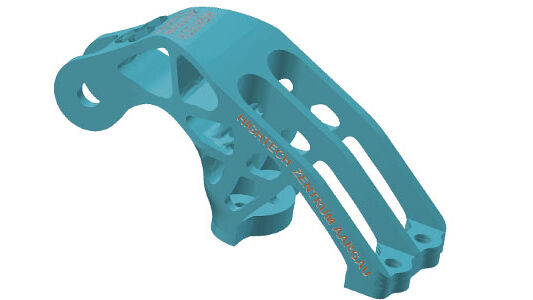
Technologie « à maturité » cherche applications
IMPRESSION MÉTALLIQUE 3D
Un séminaire de formation continue intitulé « Impression métallique 3D » a été dispensé récemment au Hightech Zentrum Aargau. Cet
événement avait pour objectif de montrer aux constructeurs quelle ligne de conduite ils doivent observer concernant cette nouvelle technologie. Renato Franchetto, mentor de l'innovation au Hightech Zentrum Aargau, a présenté brièvement les différents procédés SLM (Selective Laser Melting ou fusion sélective par laser) aux participants en guise d'introduction. Les interventions suivantes ont ensuite traité le thème central du séminaire : l'impression métallique 3D.
Connexion
Merci de l’intérêt que vous portez à nos contenus. Les abonnés de la revue spécialisée metall trouveront le Login pour l’accès intégral dans les informations légales de la version imprimée actuelle. Le mot de passe change tous les mois.
Inscrivez-vous maintenant pour lire cet article. Inscrivez-vous pour lire les différents articles et payez très facilement par carte de crédit. (CHF 5.- par article)
En tant qu’utilisateur enregistré, vous pouvez accéder à tout moment à l’article acheté.
Si - en tant que professionnel dans les domaines de la construction métallique, en acier et de façades - vous n’êtes pas encore abonné à la revue spécialisée metall, ne perdez plus une seconde et souscrivez dès à présent votre abonnement ici.
Traitement des données : l'alpha et l'oméga Felix Reinert de ProtoShape GmbH (Klingnau) a présenté les premières étapes du traitement des données. Dès le début, une chose est claire : tout dépend de la méthode de construction des objets. Moins on utilise de matériel de renforcement pour la réalisation et plus la construction est sophistiquée, plus le prix de production est bas. Pour illustrer son propos, Felix Reinert retourne au moyen-âge : les constructions gothiques livrent de nombreux arguments en faveur de directives de conception simples devant être respectées lors du développement de chaque composant. Exercice pratique : l'Airbus A330 A l'aide d'un modèle réduit modifié de la charnière d'un volet d'Airbus A330, on a démontré aux participants comment réduire le poids de plus de 25 % en modifiant la conception d'un composant et en le réalisant avec un procédé SLM. Considérés sur toute la durée de vie d'un avion, de tels gains de poids entraînent des économies de carburant non négligeables, surtout dans l'aéroDatenaufbereitung nautique. Evidemment, même dans cette industrie, les procédés SLM ne remplaceront pas les techniques traditionnelles de production de pièces industrielles et mécaniques du jour au lendemain. Cependant, le recours à des procédés de fabrication SLM doit être envisageable lorsqu'il est question de géométries complexes ou de modules au potentiel d'allègement considérable. Mentionnons ici qu'à l'heure actuelle, la fabrication par un procédé SLM n'est toujours pas approuvée pour les composants critiques de l'aéronautique. Pourtant, les grands constructeurs aéronautiques et leurs sous-traitants, de même que les autorités de l'aviation de tous pays travaillent à l'élaboration de normes correspondantes.